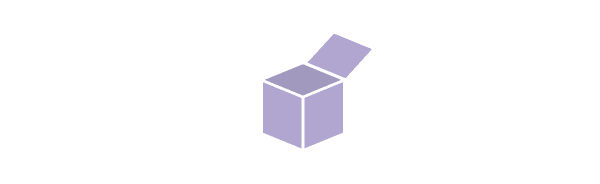
導入事例
【販売管理システムcube】
導入事例 F社
1.課題
売上は伸びているが、実際に儲かっているのかわからない。
2.ソリューション
原価管理をきっちり行うことで、商品別や得意先別の収益性を把握する。
原材料構成マスタや日報を入力することで、材料費、加工費を把握し可視化を実現。
3.効果
製造原価が把握できることで、営業スタイルも変化。
収益性の悪い商品の価格見直しや、原材料構成の見直し、あるいは取引先への価格交渉や、最低受注数を決めたり等の改善活動を行うことで、収益性が向上した。
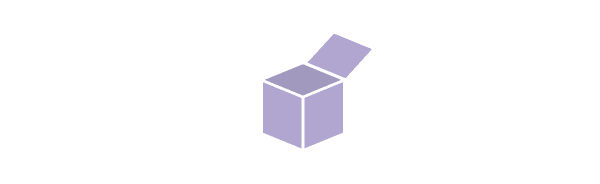
導入事例
【CUBE FACTORY 1】
導入事例 E社
1.課題
部品表をマスタ化できていないため、殆どの業務を手作業で行っており、後作業が多く非常に非効率。
生産の進捗含め全く見えていない。
2.ソリューション
取引上で使用する、顧客別の価格・仕様マスタを作成し、受注時入荷検品から始まる一連の作業をバーコードハンディターミナルを使用して行う。入口から在庫が把握できることが重要。
3.効果
システム上で在庫が可視化されることで、不良在庫が削減され、欠品も減少。物流品質が向上。
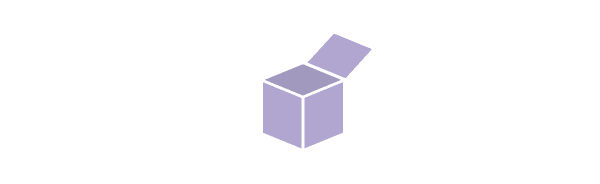
導入事例
【CUBE FACTORY 2】
導入事例 X社
1.課題
殆どの業務を手作業で行っており、後作業が多く非常に非効率生産の進捗含め全く見えていない。
2.ソリューション
取引上で使用する、顧客別の価格・仕様マスタを作成し、受注時入荷検品から始まる一連の作業をバーコードハンディターミナルを使用して行う。入口から在庫が把握できることが重要。
3.効果
システム上で在庫が可視化されることで、不良在庫が削減され、欠品も減少。物流品質が向上。
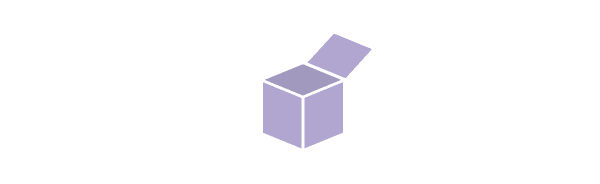
導入事例
【CUBE WMS】
導入事例 S社
1.課題
在庫が把握できていないため、各種業務にロスが発生。
不要な在庫も含め、可視化が課題
2.ソリューション
入荷検品から始まる一連の作業をバーコードハンディターミナルを使用して行う。入口から在庫が把握できることが重要。
3.効果
システム上で在庫が可視化されることで、不良在庫が削減され、欠品も減少。物流品質が向上。